Mixing Vessels
Mixing vessels are used in the brewing industry for blending and mixing different ingredients and liquids in the production of beer and other beverages. Here are some key points and content ideas that you might find useful for your project:
- 1 Mixing Vessel Overview: Start with an overview of mixing vessels and their role in the brewing process. Explain how they work, what they are used for, and the benefits of using mixing vessels in the brewing process.
- 2Mixing Vessel Design and Components: Detail the design and components of mixing vessels, including the size and shape of the vessel, the types of agitators or mixers used, and the materials used to construct the vessel.
- 3 Mixing Techniques: Discuss the different mixing techniques used in brewing, including blending of different liquids, mixing in additives such as sugar or flavorings, and the use of shear forces for emulsification.
- 4 Cleaning and Maintenance: Discuss the importance of cleaning and maintaining mixing vessels, including regular cleaning to prevent contamination and wear and tear, and the importance of proper storage and handling of the equipment.
- 5Mixing Vessels in Modern Brewing: Explore the use of modern technology in the brewing process, including automation and computer-controlled systems that allow for greater control
- 6 Common Issues and Troubleshooting: Discuss common issues that can arise with mixing vessels, such as clogging or overheating, and explore the troubleshooting steps that can be taken to resolve these issues.
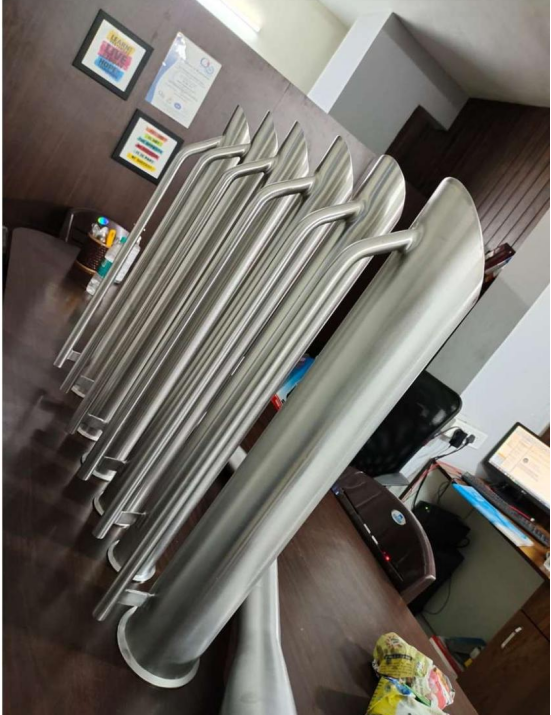